Dovetailing jig if you don't have a grinder.
You need a flat surface like the granite block I have. A piece of angle iron, sandpaper, c clamps and patience.
I did not have a piece of angle iron so I used a large block of wood. You'll get the idea with these pics hopefully. In this picture I have a square set up. With this set up this is the easiest angle. The 2 pieces of red felt were my way of marking where to c clamp this all down. Once you clamp this all down you don't want to undo it. My set up I'd have to keep cutting sandpaper to slide underneath because I couldn't slide it under the blocks of wood.
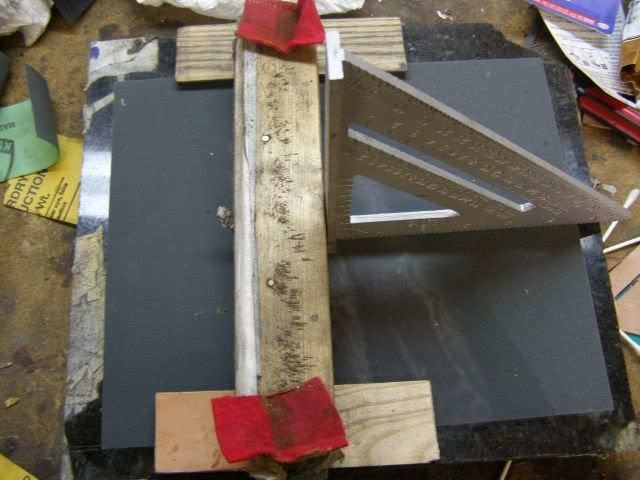
YOu could put some shims underneath to change the angle use a protractor to get the angle you want.
In use
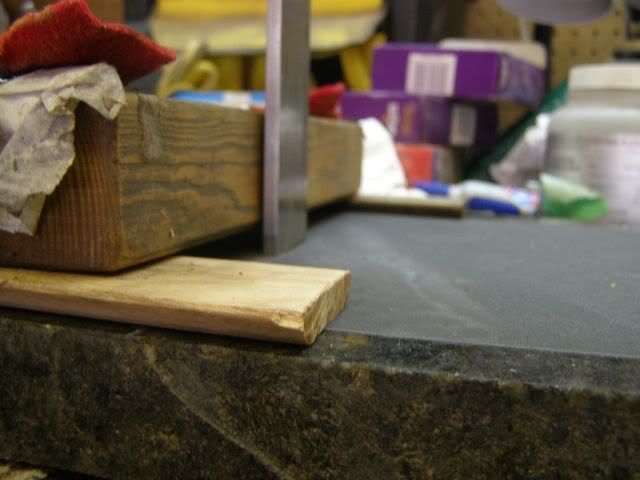
Start running it back and forth and you'll start seeing high spots.
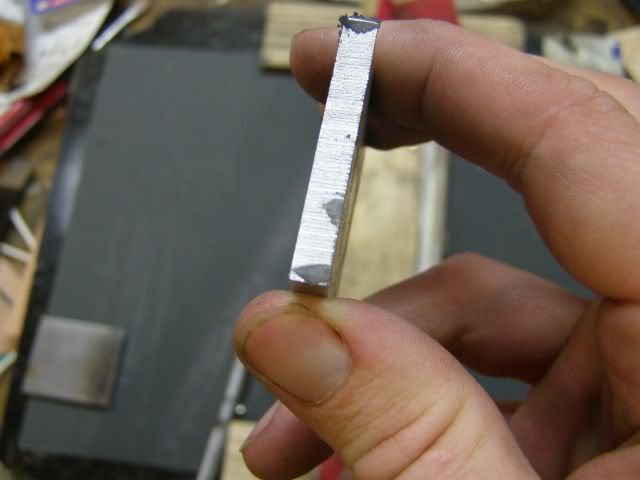
If you decide to dovetail the angle remove the bulk amount of steel with a file.
Here's a shot where I cut down the barstock to make it easier to handle
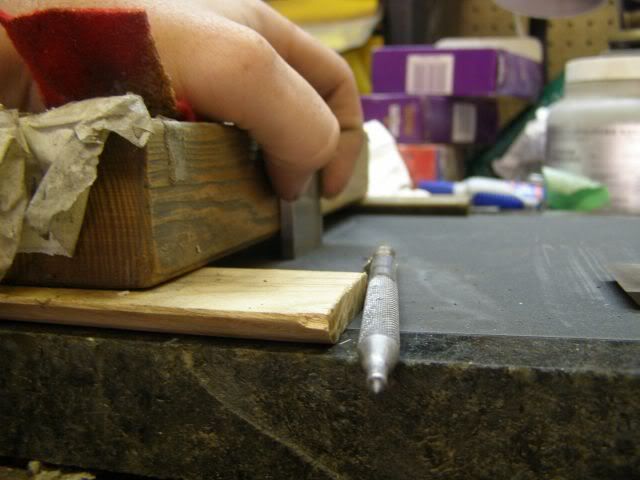
if you have any questions on this part let me know
You need a flat surface like the granite block I have. A piece of angle iron, sandpaper, c clamps and patience.
I did not have a piece of angle iron so I used a large block of wood. You'll get the idea with these pics hopefully. In this picture I have a square set up. With this set up this is the easiest angle. The 2 pieces of red felt were my way of marking where to c clamp this all down. Once you clamp this all down you don't want to undo it. My set up I'd have to keep cutting sandpaper to slide underneath because I couldn't slide it under the blocks of wood.
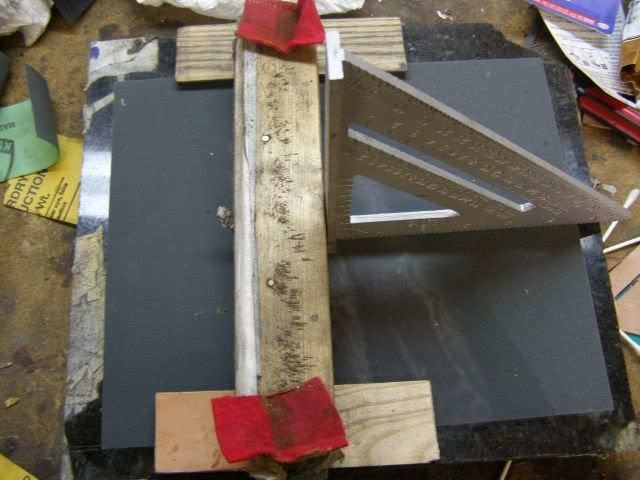
YOu could put some shims underneath to change the angle use a protractor to get the angle you want.
In use
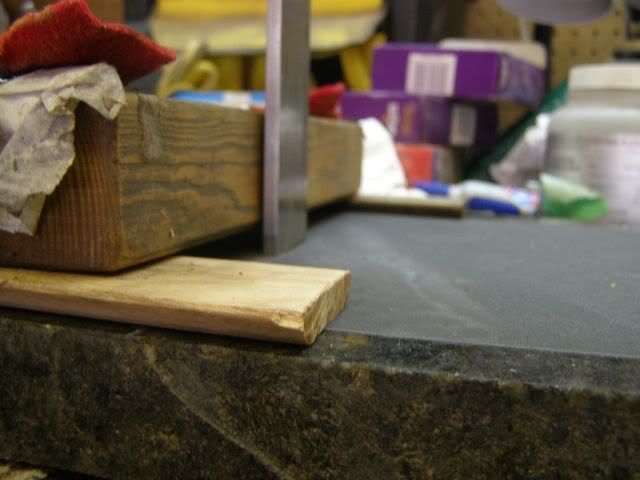
Start running it back and forth and you'll start seeing high spots.
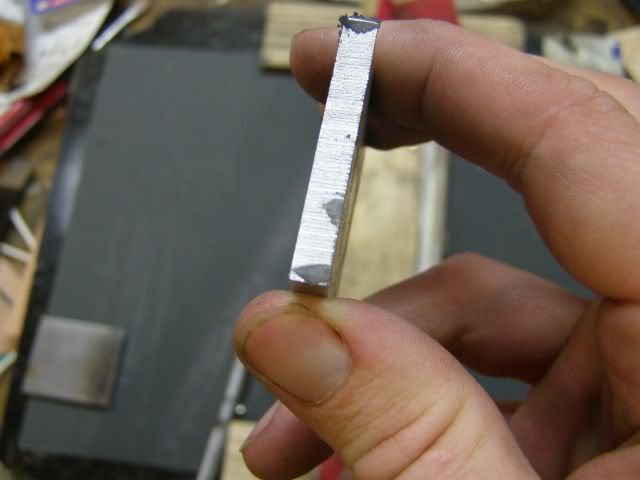
If you decide to dovetail the angle remove the bulk amount of steel with a file.
Here's a shot where I cut down the barstock to make it easier to handle
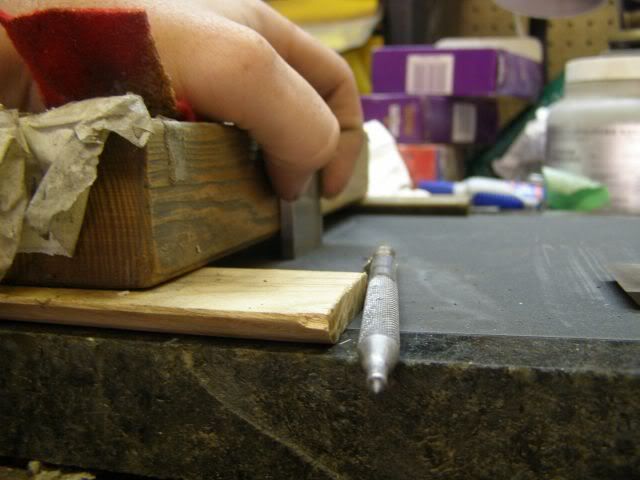
if you have any questions on this part let me know
Comment